So made a lot of progress
Almost ready to button up a pair
The baffles came out great
I made a mistake with trying to use dowels for alignment - if I build this design again I will either cut rebates with my router jig or use CNC which is coming online at Make
@Nicholas_23 said:
Did the same thing with some baffles , made a guy wished he had a planner . You got this 🤘
Same here, but a router on rails and some serious sanding time overcame that issue. The REAL missed opportunity was not watching the direction of the grain when I arranged the slats. Could have been so much more eye-catching.
@tajanes said:
Do you slightly undercut your mitered corners or just set and double measure for 45 degrees when working with baltic birch ply?
Nice project btw.
Per master builder videos, I slightly undercut the miters - about 44.5 degrees. That part worked out great, and I will do it again. No more ugly butt joints. Love my Wixley digital angle gauge.
But Chahly - Stahkist don't want speakers that look good, Stahkist wants speakers that sound good!
@Nicholas_23 said:
Did the same thing with some baffles , made a guy wished he had a planner . You got this 🤘
Same here, but a router on rails and some serious sanding time overcame that issue. The REAL missed opportunity was not watching the direction of the grain when I arranged the slats. Could have been so much more eye-catching.
Yeah, back in my Atlanta shop, I had several slab flattening jigs for my router. So happy to be able to use a honking powerful planer with good helical blades in the Make shop.
But Chahly - Stahkist don't want speakers that look good, Stahkist wants speakers that sound good!
Don,
I see from your pics you glued your project using band clamps- any recommendations? thx. I’ve always just butt jointed using clamps and right angle square.
I used these Harbor Freight strap clamps with 90 degree corners. Worked pretty good, although you still need to check for squareness for prefect results.
Those are great! I decided to use only birch, but tried to get a little variation between the strips. Moving into a new house and haven't had much time for these. I think that I'm going to pay someone to cut the driver recesses with the CNC at make. What do y'all think? Is $100 ok compensation for that?
But Chahly - Stahkist don't want speakers that look good, Stahkist wants speakers that sound good!
There is nothing like moving into a new house and getting settled to slow you down!
I was very dissatisfied with the overall build quality of the folded line, (lots of gorilla glue and caulk)
so I needed to redo it much better. Obviously, the best method of joining is to route a 1/2" x 1/4" deep rabbet into the side for the line plenum.
I decided the way forward was to learn the CNC router X-Carve, which we have at Make
Not too difficult, using Easel, my first test came out almost perfect.
Now I can start the same with my new 3/4 BB pieces!
But Chahly - Stahkist don't want speakers that look good, Stahkist wants speakers that sound good!
After the test cuts on cheap plywood, I finally got around to working with 3/4 BB (at $120 per 5x5 sheet, it's precious!) - everything fit well, but not perfect. The 1/2 BB I measured at 11.8mm or so, but the "dirty" cuts by the upcut bit left a little crap in the slots. I had specified 12.1mm width, but that required a little rubber hammer work to mate the pieces. Looks like I'll need to increase that to 12.2mm for the next pieces.
Man oh man, I am SO digging the X-Carve CNC. I setup the machine to cut the rabbets and used the table saw to cut the plenum 1/2 BB pieces while the CNC worked.
Now I realize that cutting baffles perfectly is child's play for this machine. Another big area of trauma for me!
But Chahly - Stahkist don't want speakers that look good, Stahkist wants speakers that sound good!
I wonder if dropping the feed down would cut down on the chipout. Not that it matters much on internal stuff like that and it seems to clean up decently anyway.
This got me searching for a local maker space. It appears there is a local one that just acquired a building and is trying to get off the ground. I might have to help out.
@DrewsBrews said:
I wonder if dropping the feed down would cut down on the chipout. Not that it matters much on internal stuff like that and it seems to clean up decently anyway.
This got me searching for a local maker space. It appears there is a local one that just acquired a building and is trying to get off the ground. I might have to help out.
I've been there for about 18 months now. Really great bunch of peeps. People come up now and say "I hear that you are the speaker guy".
But Chahly - Stahkist don't want speakers that look good, Stahkist wants speakers that sound good!
Scott Hinson on FB Diy Loudspeaker Pad posted a white paper where he concluded that TLs require a much larger box than a BR for the same response. I worked an example today with a Rival 176CP in a BR and MLTL. Simmed responses were pretty much the same.
But Chahly - Stahkist don't want speakers that look good, Stahkist wants speakers that sound good!
SO after many troubles, I am ready to glue the right side on, and find that I have a 1/8 inch gap between the plenum boards (which are 1/2 inch BB) and the right side. Obviously, if I screw this up, the TL speaker is of no use. My choices are self stick closed cell weather proofing, or Gorilla Glue construction glue that can fill gaps. Any advice?
But Chahly - Stahkist don't want speakers that look good, Stahkist wants speakers that sound good!
gorilla glue or thick bead of contruction adhevise will fill in the gap and help it to stick. cover it with generous helping of caulk - doesn't need to look pretty on the inside, but make the joint airtight
Rather than just relying on glue/caulk to seal a 1/8th gap, add glue/construction adhesive on both sides of some 1/16th plastic or craft board. Then you're just asking the glue/caulk to fill in about 1/32" per side.
My old Ohio Menards had 1/32 and 1/16 inch Basswood boards but my Michigan Menards doesn't carry it. I've also bought 1/16" plastic cutting boards (3 pack on Amazon) for making certain jigs, but not sure how good the glue would adhere.
Thanks guys! All good suggestions. One other solution occurred to me, Use 2 or more layers of veneer on the side board. But the real solution I found at Michaels. Basswood craft sticks in various sizes that are about 5/64 thick. So just about perfect for glue up. Pictures tomorrow when I can get back to my shop (in a corner of the garage).
But Chahly - Stahkist don't want speakers that look good, Stahkist wants speakers that sound good!
It turned out that once I clamped down the last side panel, the gap between the plenum was less than 1/8 inch, so good old Gorilla Glue cam to the rescue. Put on a little more than necessary, but I think I got a good seal. Really won't know until I do impedance tests.....
But Chahly - Stahkist don't want speakers that look good, Stahkist wants speakers that sound good!
I have a bunch of veneer that I moved with me from Atlanta. Decided that teak would be a nice contrast with the baltic birch butcher block baffle previously in this thread. Turned out that 1/2 sheet would just fit this project. I had used Heatlock for many projects, but thought I'd try Titebond II for this. Worked pretty great.
and 1 other.
But Chahly - Stahkist don't want speakers that look good, Stahkist wants speakers that sound good!
Comments
So made a lot of progress
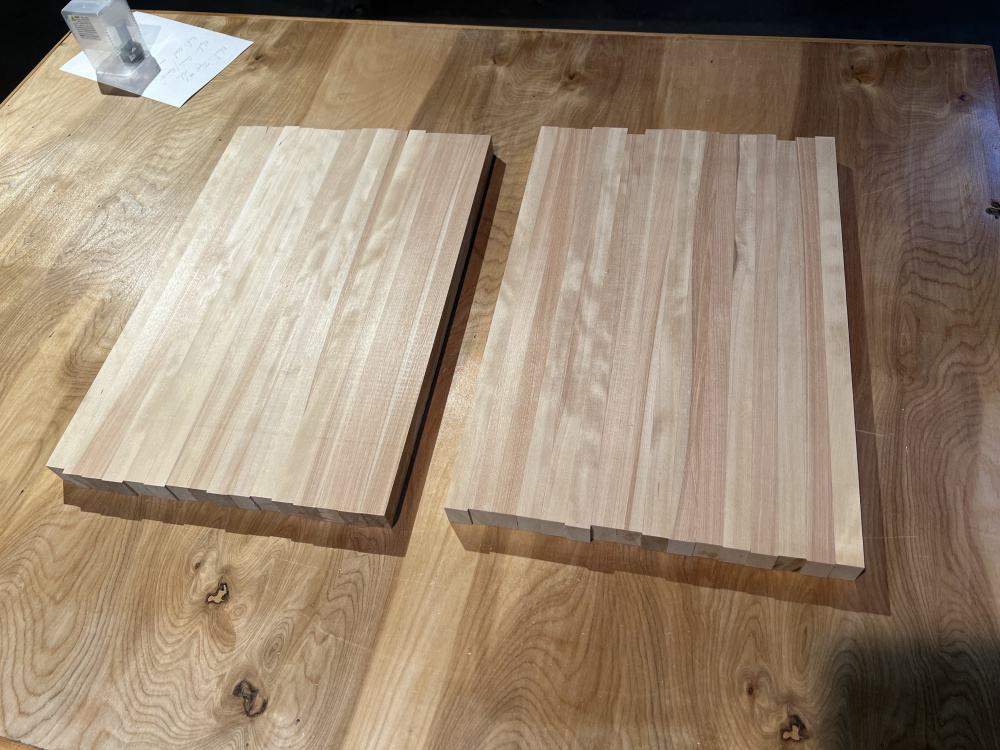
Almost ready to button up a pair
The baffles came out great
I made a mistake with trying to use dowels for alignment - if I build this design again I will either cut rebates with my router jig or use CNC which is coming online at Make
You can see some of my alignment fixups in the side view
(https://diy.midwestaudio.club/uploads/editor/a4/pxvzr59ot7l4.jpeg "")
(https://diy.midwestaudio.club/uploads/editor/rw/gn1fst8zf60p.jpeg "")
Do you slightly undercut your mitered corners or just set and double measure for 45 degrees when working with baltic birch ply?
Nice project btw.
Same here, but a router on rails and some serious sanding time overcame that issue. The REAL missed opportunity was not watching the direction of the grain when I arranged the slats. Could have been so much more eye-catching.
Per master builder videos, I slightly undercut the miters - about 44.5 degrees. That part worked out great, and I will do it again. No more ugly butt joints. Love my Wixley digital angle gauge.
Yeah, back in my Atlanta shop, I had several slab flattening jigs for my router. So happy to be able to use a honking powerful planer with good helical blades in the Make shop.
Don,
I see from your pics you glued your project using band clamps- any recommendations? thx. I’ve always just butt jointed using clamps and right angle square.
I used these Harbor Freight strap clamps with 90 degree corners. Worked pretty good, although you still need to check for squareness for prefect results.
https://harborfreight.com/1-inch-x-15-ft-ratcheting-band-clamp-66220.html
Thx, and about $9.50 less than from Amazon with their ‘free shipping’
Those are great! I decided to use only birch, but tried to get a little variation between the strips. Moving into a new house and haven't had much time for these. I think that I'm going to pay someone to cut the driver recesses with the CNC at make. What do y'all think? Is $100 ok compensation for that?
There is nothing like moving into a new house and getting settled to slow you down!
I was very dissatisfied with the overall build quality of the folded line, (lots of gorilla glue and caulk)
so I needed to redo it much better. Obviously, the best method of joining is to route a 1/2" x 1/4" deep rabbet into the side for the line plenum.
I decided the way forward was to learn the CNC router X-Carve, which we have at Make
Not too difficult, using Easel, my first test came out almost perfect.
Now I can start the same with my new 3/4 BB pieces!
After the test cuts on cheap plywood, I finally got around to working with 3/4 BB (at $120 per 5x5 sheet, it's precious!) - everything fit well, but not perfect. The 1/2 BB I measured at 11.8mm or so, but the "dirty" cuts by the upcut bit left a little crap in the slots. I had specified 12.1mm width, but that required a little rubber hammer work to mate the pieces. Looks like I'll need to increase that to 12.2mm for the next pieces.
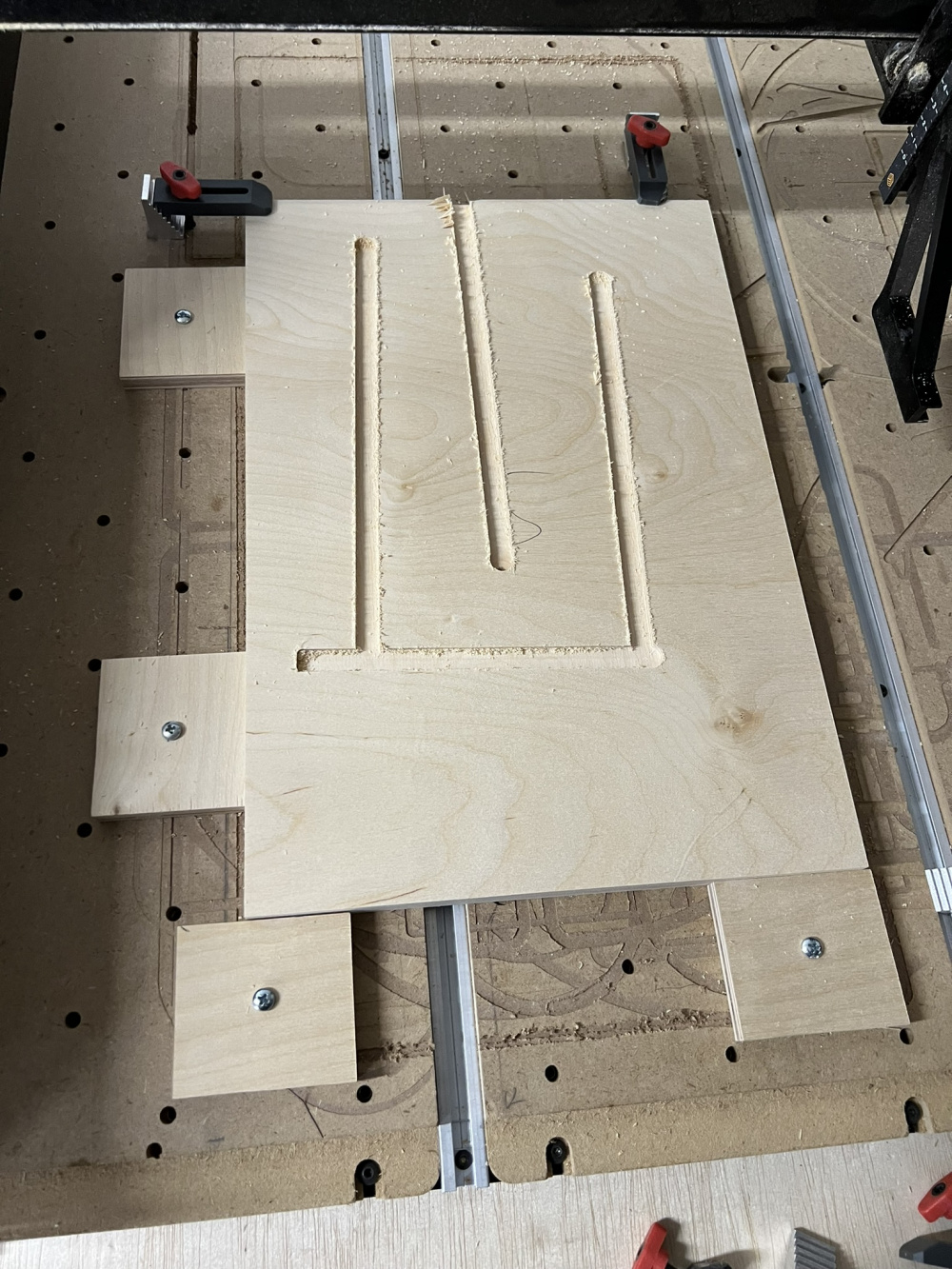
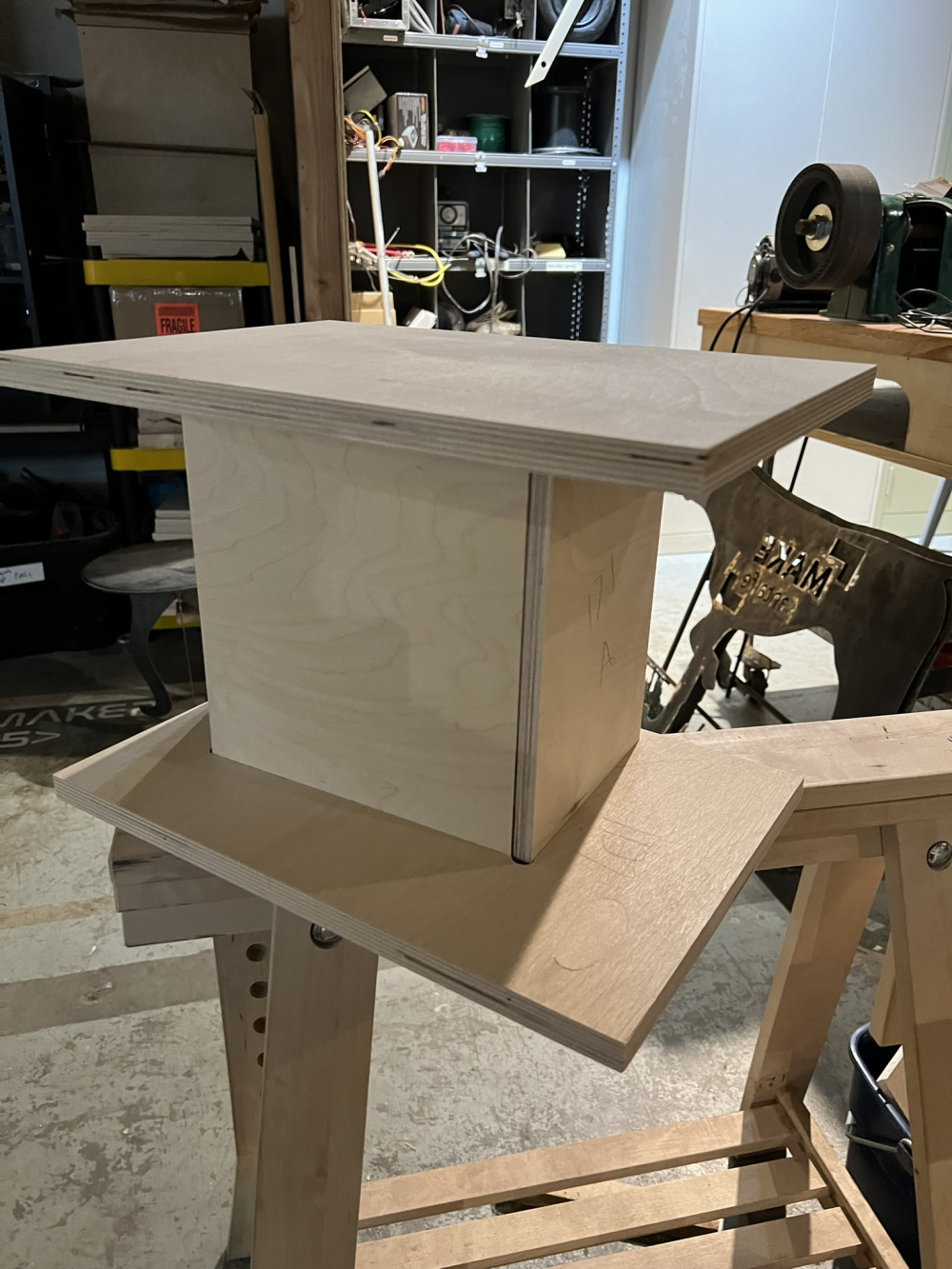
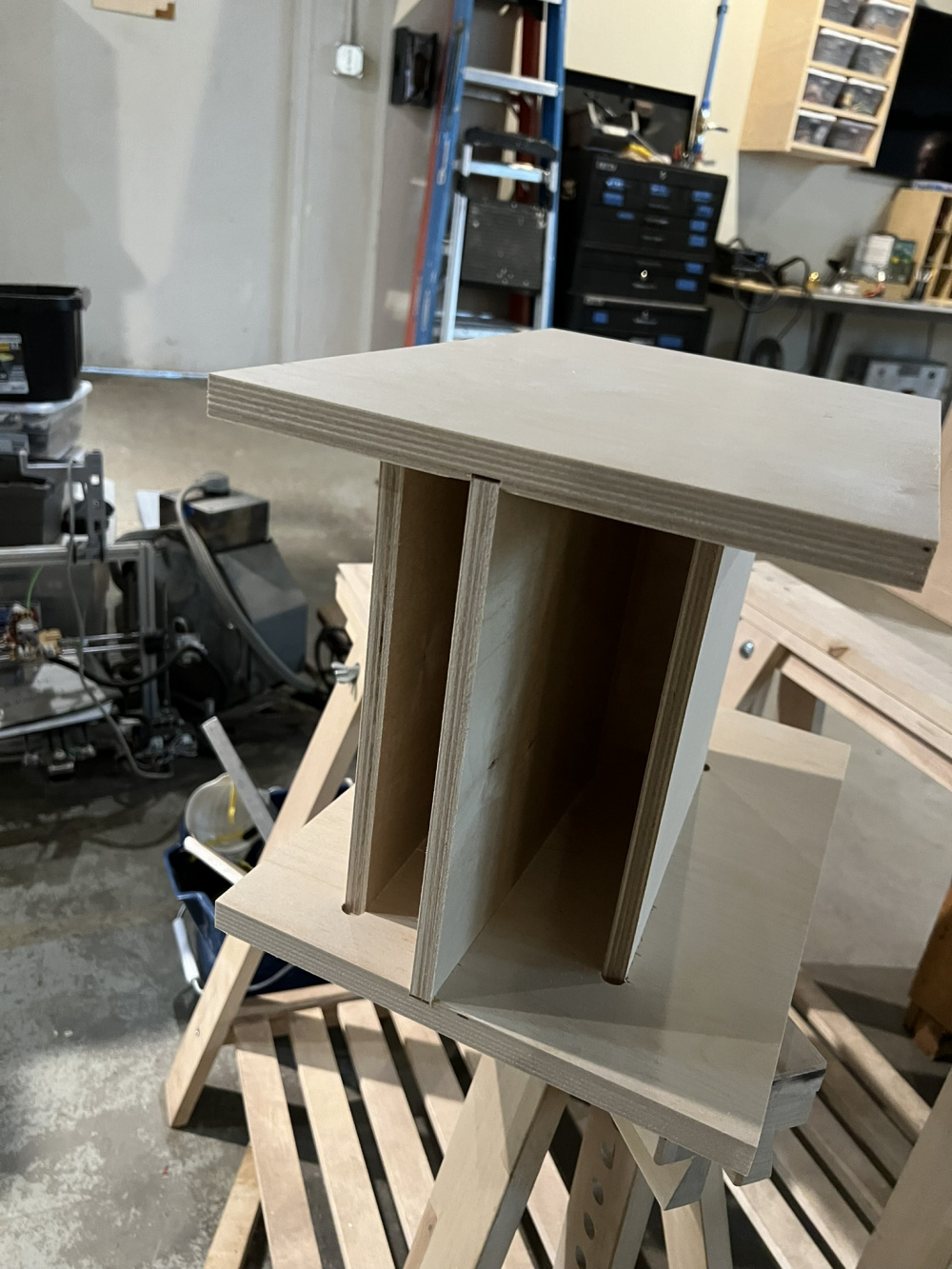
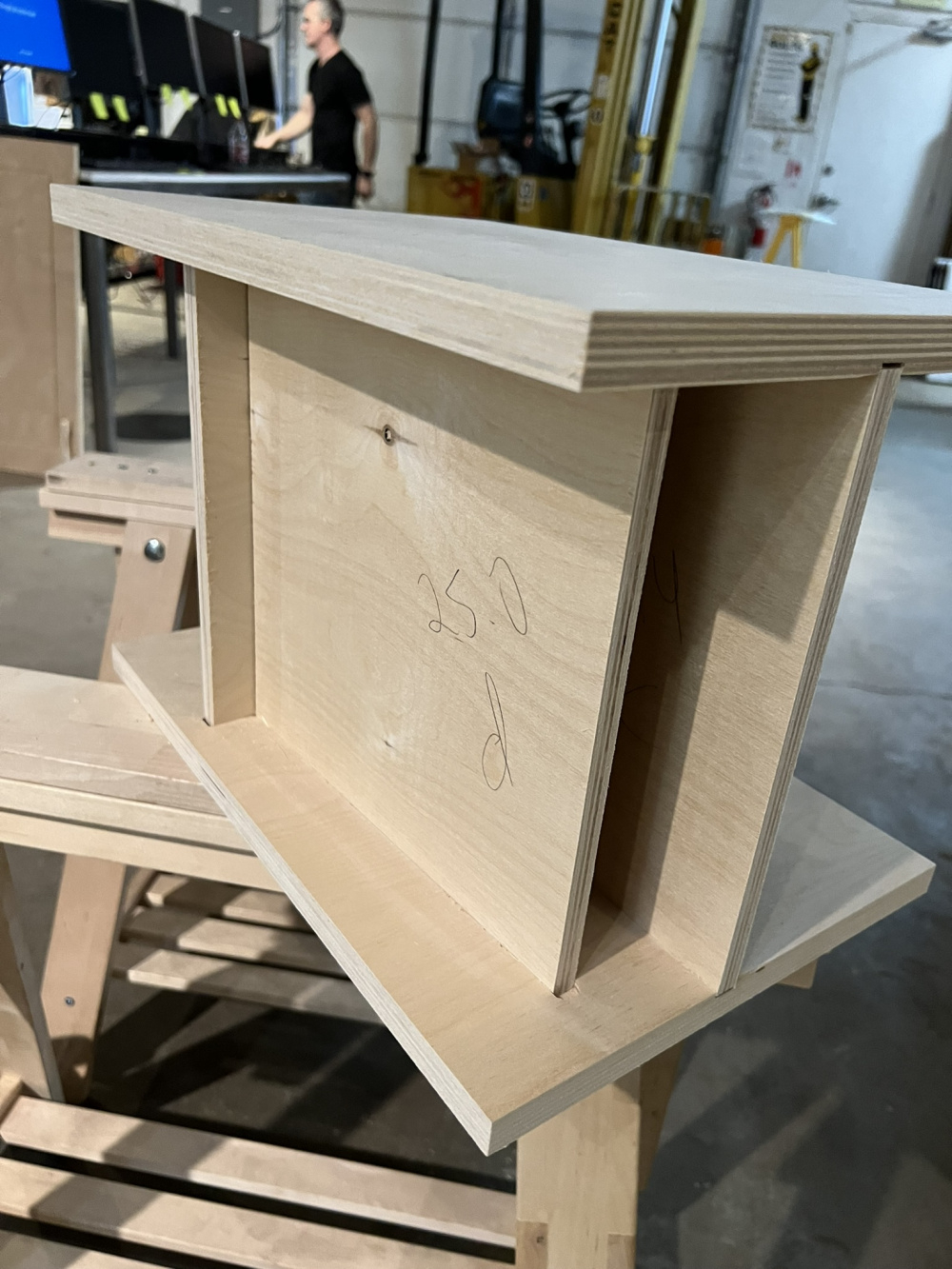
Man oh man, I am SO digging the X-Carve CNC. I setup the machine to cut the rabbets and used the table saw to cut the plenum 1/2 BB pieces while the CNC worked.
Now I realize that cutting baffles perfectly is child's play for this machine. Another big area of trauma for me!
I wonder if dropping the feed down would cut down on the chipout. Not that it matters much on internal stuff like that and it seems to clean up decently anyway.
This got me searching for a local maker space. It appears there is a local one that just acquired a building and is trying to get off the ground. I might have to help out.
I've been there for about 18 months now. Really great bunch of peeps. People come up now and say "I hear that you are the speaker guy".
Scott Hinson on FB Diy Loudspeaker Pad posted a white paper where he concluded that TLs require a much larger box than a BR for the same response. I worked an example today with a Rival 176CP in a BR and MLTL. Simmed responses were pretty much the same.
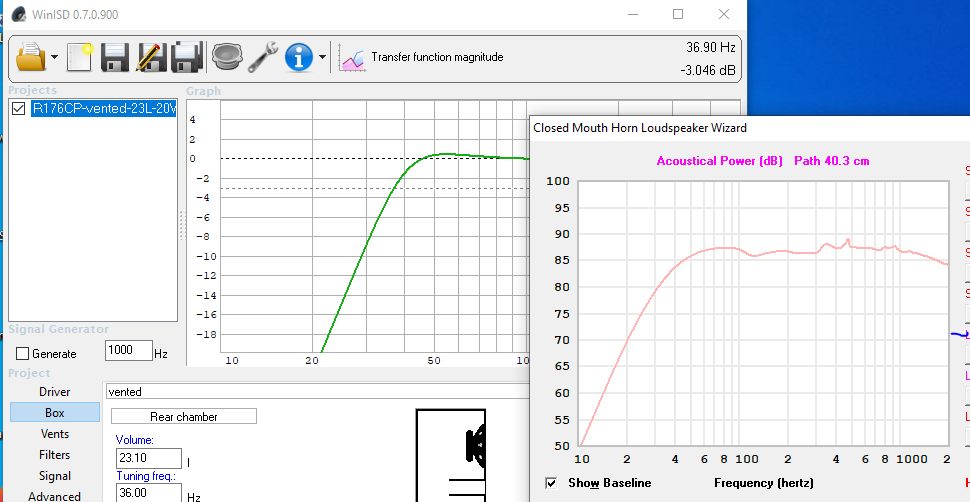
Measured vs sim results, I guess?
Those are your two charts above, overlayed on same scale/aspect.
ok, thanks! sheesh.
SO after many troubles, I am ready to glue the right side on, and find that I have a 1/8 inch gap between the plenum boards (which are 1/2 inch BB) and the right side. Obviously, if I screw this up, the TL speaker is of no use. My choices are self stick closed cell weather proofing, or Gorilla Glue construction glue that can fill gaps. Any advice?
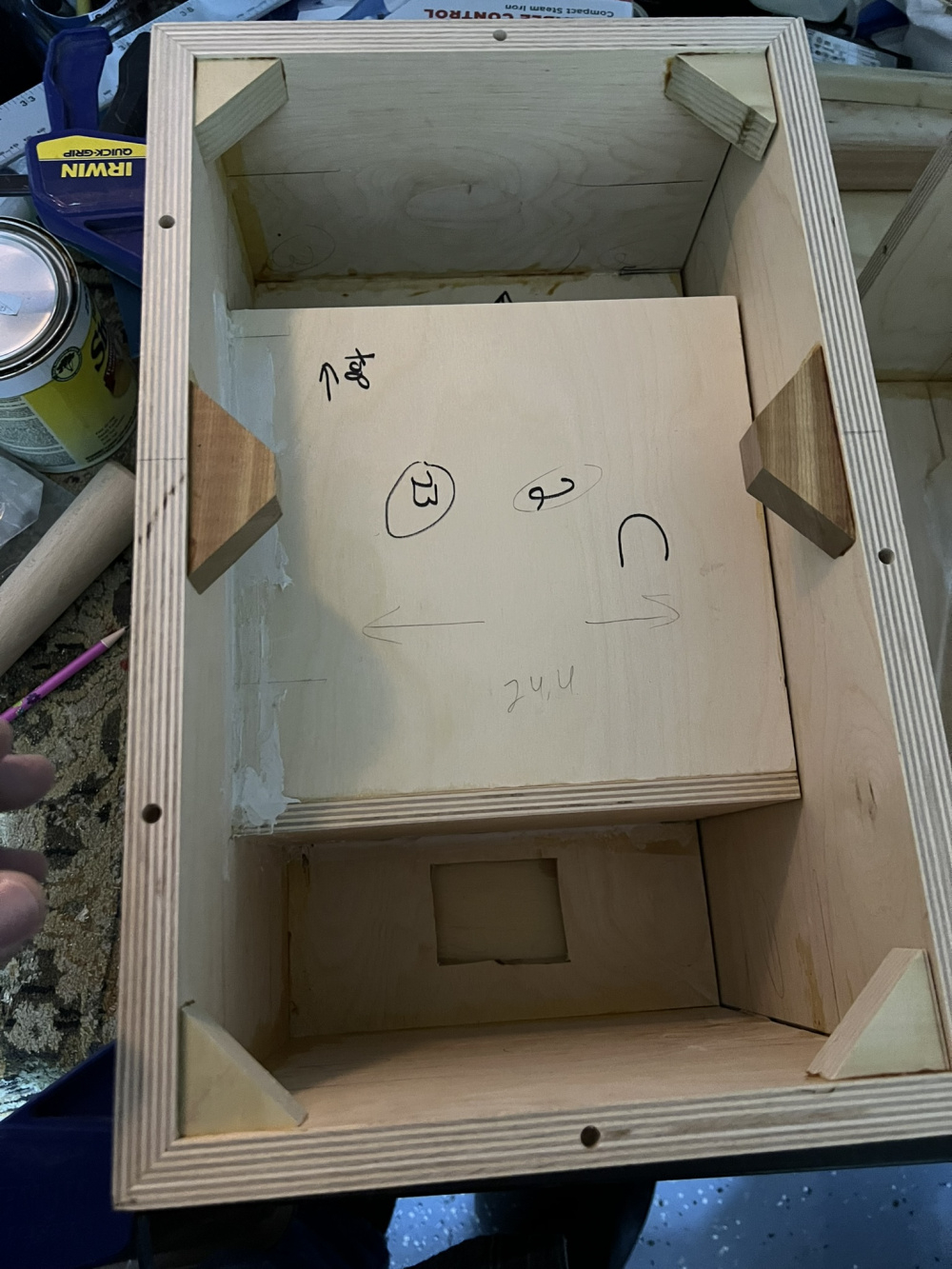
Silicone sealeant (or the non silicone variety - use whatever to stick, and then the caulk to make it air tight.
gorilla glue or thick bead of contruction adhevise will fill in the gap and help it to stick. cover it with generous helping of caulk - doesn't need to look pretty on the inside, but make the joint airtight
Rather than just relying on glue/caulk to seal a 1/8th gap, add glue/construction adhesive on both sides of some 1/16th plastic or craft board. Then you're just asking the glue/caulk to fill in about 1/32" per side.
My old Ohio Menards had 1/32 and 1/16 inch Basswood boards but my Michigan Menards doesn't carry it. I've also bought 1/16" plastic cutting boards (3 pack on Amazon) for making certain jigs, but not sure how good the glue would adhere.
Yeah add a shim as a4eaudio mentions, that should prevent worries is glue or caulk shrinking over time.
Mix up some epoxy and add sawdust to thicken it. It will be airtight and structural.
Thanks guys! All good suggestions. One other solution occurred to me, Use 2 or more layers of veneer on the side board. But the real solution I found at Michaels. Basswood craft sticks in various sizes that are about 5/64 thick. So just about perfect for glue up. Pictures tomorrow when I can get back to my shop (in a corner of the garage).
It turned out that once I clamped down the last side panel, the gap between the plenum was less than 1/8 inch, so good old Gorilla Glue cam to the rescue. Put on a little more than necessary, but I think I got a good seal. Really won't know until I do impedance tests.....
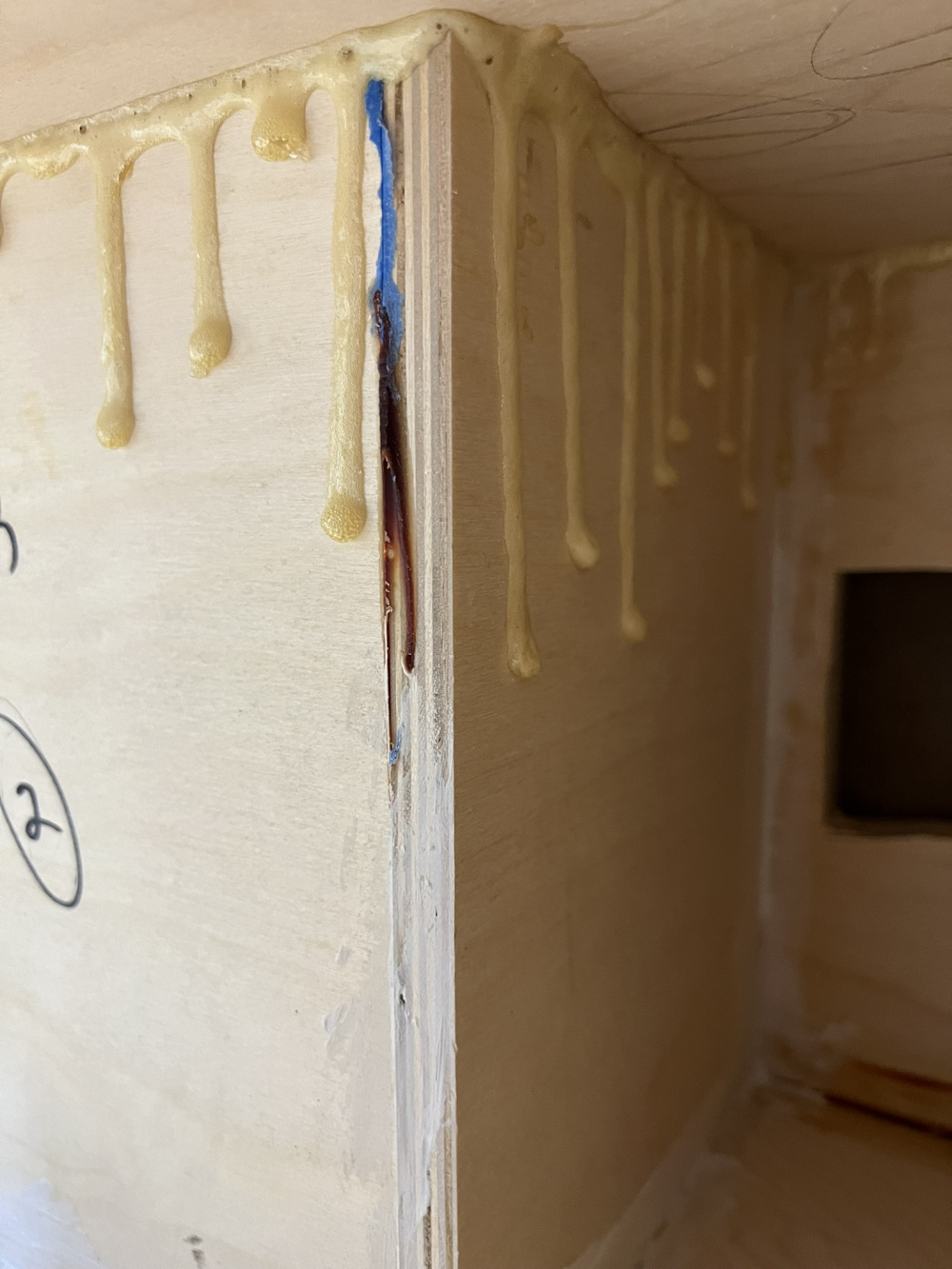
I have a bunch of veneer that I moved with me from Atlanta. Decided that teak would be a nice contrast with the baltic birch butcher block baffle previously in this thread. Turned out that 1/2 sheet would just fit this project. I had used Heatlock for many projects, but thought I'd try Titebond II for this. Worked pretty great.

Looking great!
I thought that was Zebrawood, regardless, looking purdy good dude🤘🏼😎
Those are going to be stunning!